Decomposing scrap tyres represent a big environmental challenge. In addition to taking up lots of space and looking unsightly, tyre waste also releases all sorts of toxins into the natural environment when landfill lining becomes damaged. Fortunately, thanks to modern tyre to oil plants, it’s now possible to convert waste rubber into useful end products. In the past, converting tires into oil was not commercially viable, so a lot of tyre waste was sent for incineration. One of the key differences between a tyre incineration plant and waste tyre to oil plant is that the later does not emit any toxins into the atmosphere.
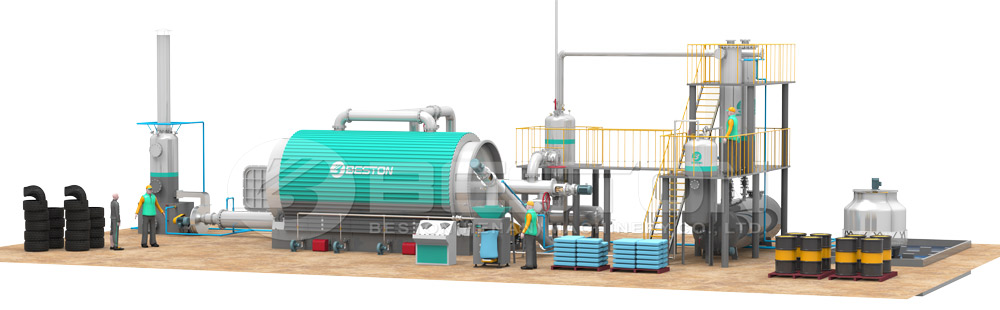
Tyre to Oil Plant
There are now waste recycling businesses across the globe investing in the best tyre to oil machines. Such machines extract fuel oil, steel wire, carbon black, and combustible gas from scrap tyres. The best machine designs are fully automatic, energy-efficient, and eco-friendly. They also ensure the highest possible pyrolysis oil yields from rubber waste and have long service lifespans.
In a fully automatic pyrolysis plant, rubber waster is automatically fed into the main reactor on a continual basis and the end products are automatically discharged and collected round-the-clock. Meanwhile, with a batch tyre to oil plant, the reactor has to be cooled down between different batches of tyre waste so the end products can be manually collected. Semi-continuous rubber pyrolysis plants are also available.
There are several factors that businesses need to take into account before investing in a tyre to oil machine including budget restraints and space limitations. Specifications to compare when looking at technical datasheets include working method, reactor size, reactor patter, heating materials, total power, cooling method, lifespan, daily capacity, operating pressure, area requirements, running costs, and price. Fully continuous pyrolysis plants have the highest output capacities with larger models able to process over 24 tons of tyre waste each day.
When it comes to calculating the qualities of different end products that can be extracted from scrap types, it’s helpful to consider the percent yield figures from a typical road tyre. A typical tyre is comprised of 55% tire oil, 25% carbon black, 8% combustible gases, and 12% steel wire. This means that from 100 tons of tyre waste you can expect to extract around 55 tons of fuel oil via pyrolysis. Also, you can see a small pyrolysis machine here.
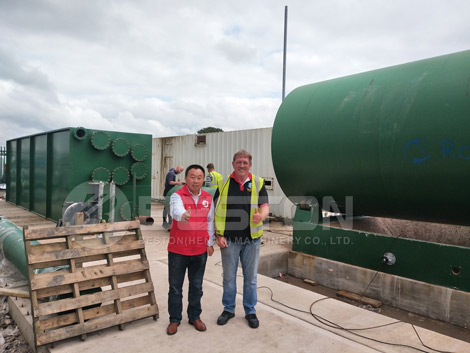
BLL-16 Tyre Pyrolysis Machine in United Kingdom
All of the end products from tyre pyrolysis have a multitude of applications. Tyre oil, for instance, can be sold as fuel to heavy industries or it can be converted into more refined fuels, like gasoline and diesel, using an oil distillation plant. Carbon black meanwhile can be sold to the pharmaceutical industry and fertilizer industry. It can also be converted into fuel briquettes. The combustible gas produced is generally used to fuel the reactor in a tyre pyrolysis plant, but it can also be collected in tanks and sold in the global market space. Finally, all of the steel wire extracted can be sold directly to metal factories where it is melted down and converted into steel bars for the construction industry.