Charcoal is the solid product that is the result of the decomposition of any organic material through the application of heat. Biochar is the charcoal-like material that is made through biomass pyrolysis plant in a process that does not use oxygen. It is a material that can be crushed into smaller pieces and mixed in the soil where it improves the properties of the soil and gives better plant growth if the biochar is enhanced with microorganisms and nutrients.
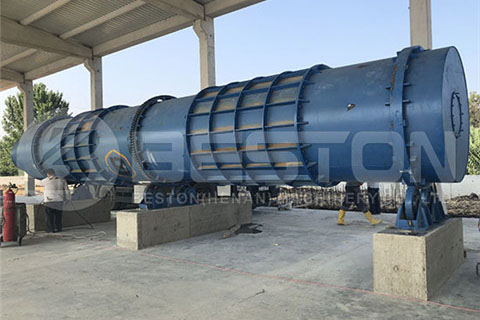
Biochar Production Plant in Turkey
The biochar production equipment involves pyrolysis which in broad terms is the breakdown of biomass under heat and in an environment that has limited oxygen. In this process, the biomass is converted into char, a solid residue that is rich in carbon, as well as gases and liquids. Biomass used for biochar production will have five components, cellulose, lignin, hemicellulose, minerals and water in different proportions that will depend on the source from which the biomass is obtained. Freshly cut biomass will have a high content of water that can be between 40 and 60 percent and this has to be first removed before the production of biochar is commenced.
Water gets removed from biomass when temperatures exceed 100 degrees Centigrade. Once the temperatures reach 150 degrees, the biomass starts to disintegrate and water that is chemically bound will be released along with volatile organic compounds and carbon dioxide. Driving out all the water from biomass needs a lot of energy and if this drying process is separated it can help to give low emissions and high quality and yield of biochar. Ideal moisture content has to be below 15 percent before the biomass is subjected to biomass pyrolysis.
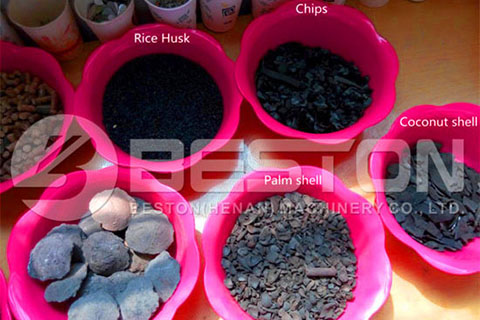
Biomass Charcoal
Further heating of the biomass to temperatures between 200 and 280 degrees will result in the breakdown of the chemical bonds of the biomass constituents. At this stage, volatile organic compounds are released, along with CO2 and CO which come from the breakdown of the cellulose elements of the biomass. As temperatures increase the biomass exudes combustible mixtures of hydrogen, hydrocarbons, and tars. The pyrolysis then becomes exothermic and the process becomes self-sustaining, that produces temperatures of about 400 degrees. At this temperature, the residue is oxygen depleted and carbon enriched charcoal.
In actual practice, heat is lost in the pyrolysis region and this requires some external heat to maintain temperatures. At the end of the exothermic stage of the pyrolysis, you get the maximum yield of 5 percent ash, 30 percent of volatiles and the balance as fixed carbon. Further heating is needed to remove the volatiles and increasing the carbon content of the biochar. At 550 to 600 degrees the biochar will increase to 85 percent. Biochar yield finally is 30 percent of the weight of the dried biomass that is used as feedstock in the charcoal carbonization furnace.
Air and steam are then introduced to initiate activation of the surface of the biochar. Gas is also produced that is relatively clean and can be used for the generation of electricity. Biomass that is treated with various compounds before being submitted for pyrolysis can alter the quality of the biochar produced.